Overview Conveyor belts are an essential part of many warehouses and factories, moving goods from...
Conveyors & Conveyor Parts
Explore the full range of conveyors and parts available at Span Tech. From complete systems to essential components, we have everything you need for efficient material handling.
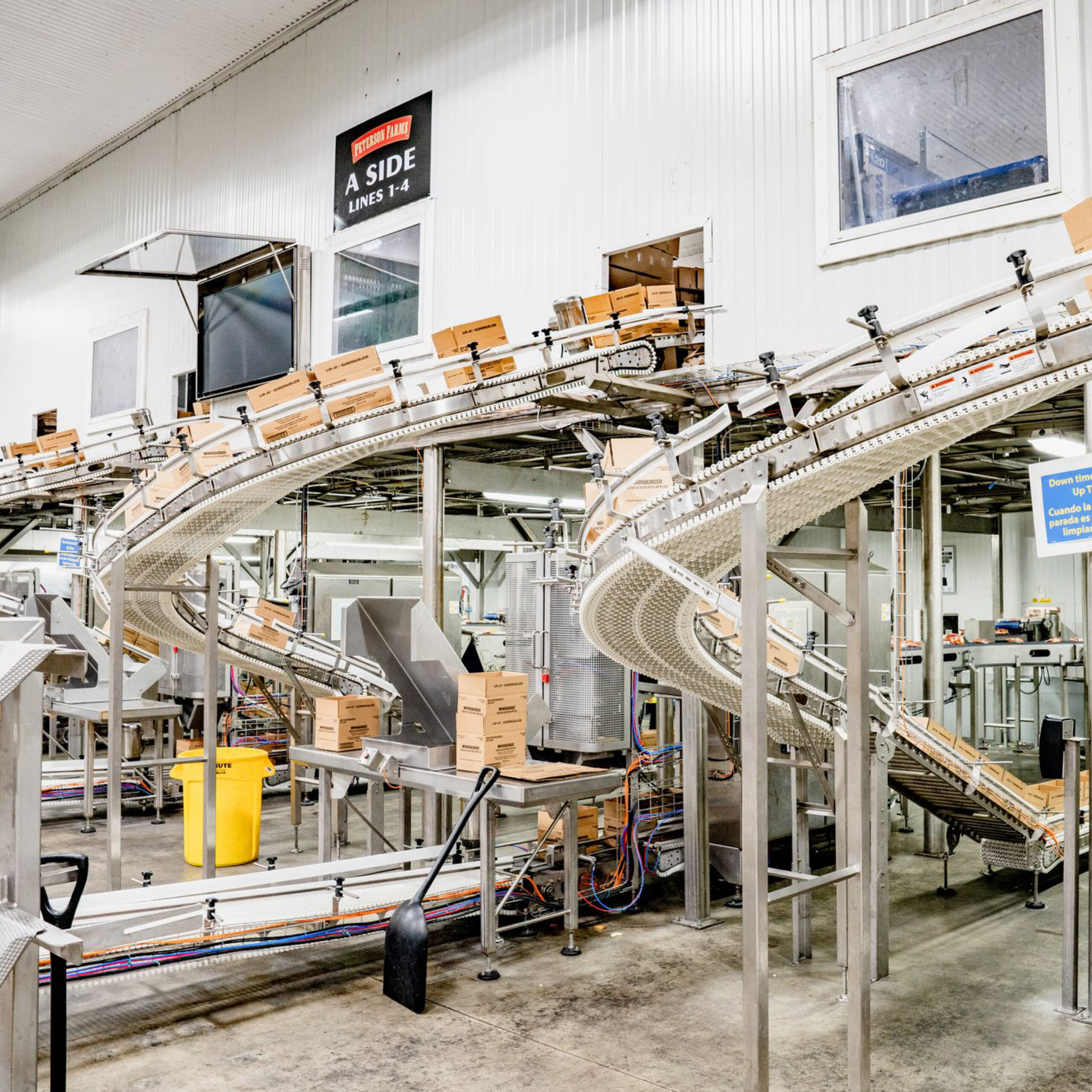
Are Worn Out Conveyor Guide Rail Systems Slowing Down Your Production Line Efficiency?
Overview Conveyor guide rail systems are an integral part of the production line. Their job is to...
Common Conveyor Belt Problems & How To Fix Them
With many conveyor systems running 24/7 in critical operations, common conveyor belt problems can...
Why Molded Plastic Conveyor Belt Parts Are Better Than Metal
There's no doubt that plastic has been a game-changer for countless industries since its invention...
5 Manufacturing Industry Trends for 2022
As we've embarked on this new year, there are many exciting challenges and advancements to look...
Conveyor Belt Safety: The Eight Do’s and Don’ts of Operating Automated Conveyor Systems
If your business utilizes automated conveyor systems in any way, conveyor belt safety should...
Three Considerations When Designing Conveyor Sortation Systems
Overview Eventually, you're going to need a new conveyor sortation system. Whether you're...
How Beverage Industry Trends Are Changing Beverage Conveyor Systems
Overview Forecasts indicate that the beverage industry will continue to expand through the...
Six Benefits of Using Food Conveyor Systems in the Food Industry
Food processing and packaging require a great deal of material handling. Raw materials and...
Conveyor Sortation Systems That Meet the Needs of E-Commerce Businesses
The e-commerce explosion has forever changed how business works. Brick-and-mortar stores no longer...